What Is Post-Molding Processes?
Post-molding processes, also known as secondary processing or finishing, involve various techniques used to enhance and protect injection-molded plastic parts. These post-processing methods can add functionality or create a uniform appearance, tailored to meet specific customer requirements.
There is a wide range of secondary operations available for product customization. Our experts, with decades of combined experience in the injection molding industry, guide customers through every step of the process—from design and molding to finishing operations.
Common injection molding secondary processes include painting, welding, post-mold machining, assembly, and packaging. Each of these techniques plays a crucial role in ensuring the final product meets the highest standards of quality and performance.
Why Choose Rockeypad for Post-Molding Processes of Silicone Keypads?
Achieving top-quality silicone keypads requires a deep understanding of resin properties, assembly methods, and finishes. At Rockeypad, we provide detailed insights to help you achieve optimal results and offer tailored solutions that fit your specific requirements.
- Expertise in Materials: Rockeypad excels in both silicone and Liquid Silicone Rubber (LSR) materials. Our extensive knowledge enables us to recommend and apply the most effective post-molding processes for superior silicone keypad performance.
- Precision and Consistency: Our advanced post-molding techniques ensure that every silicone keypad maintains precise and consistent quality, enhancing both functionality and appearance.
- Customized Solutions: Recognizing the diverse needs across various industries, we offer bespoke post-molding processes that cater specifically to your unique requirements, ensuring your silicone keypads are perfectly suited to their applications.
- State-of-the-Art Facilities: Rockeypad is equipped with modern technology and facilities, allowing us to perform a wide range of post-molding treatments efficiently and with exceptional quality.
- Quality Assurance: We adhere to rigorous quality control protocols throughout the post-molding process to guarantee that every silicone keypad meets the highest standards of excellence.
- Comprehensive Services: From surface treatments and coloring to assembly and packaging, Rockeypad provides a full spectrum of post-molding services, streamlining the process and saving you time and resources.
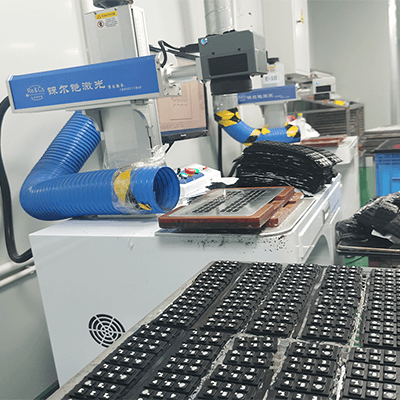
Laser Etching
Laser etching has become a standard technique in silicone keypad manufacturing, providing significant advantages in both efficiency and effectiveness. This process involves the use of a high-powered laser to remove layers of paint from the keypad surface, resulting in precise and durable markings.
Traditional marking methods often come with high consumable costs, posing challenges and additional expenses for keypad customization. Laser marking, on the other hand, eliminates the need for consumables, leading to substantial cost savings for customers. At Silkeypad, our computer-controlled laser marking machines ensure ease of operation, stability, and exceptional precision. Additionally, our laser marking process boasts superior efficiency compared to conventional methods, making it an ideal choice for customizing silicone keypads.
Silkscreen Printing
Our silkscreen printing uses proprietary silicone inks to apply positive and reverse graphics on silicone rubber keypads. This process ensures a durable bond during curing, resulting in graphics that maintain their integrity throughout the keypad's lifespan under standard industry conditions.
High-quality graphics are crucial for user perception and product aesthetics. A well-designed keypad improves both visual appeal and functionality. We offer expert recommendations to optimize the design and graphics of silicone rubber keypads.
Multiple colors require separate screens, which may increase costs. Silkscreen printing is effective for flat keytop surfaces but may not be suitable for convex or concave shapes. For backlighting applications, positive or negative silkscreen printing on clear or milky-white silicone offers a cost-effective alternative to laser etching.
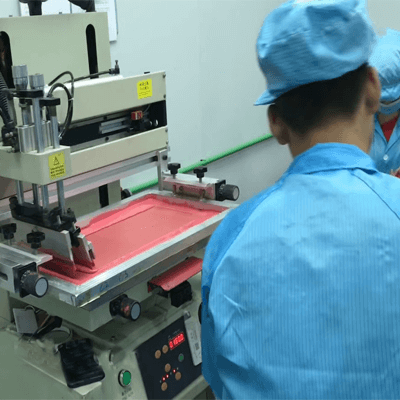
Color Matching
At Rockeypad, we leverage the globally recognized Pantone Matching System (PMS) to ensure precise color matching for both silicone materials and applied graphics. This standardized system enables us to achieve accurate color reproduction, whether for opaque or translucent silicone.
Our capabilities extend to producing silicone in both opaque and translucent colors. The level of pigment used during the molding process determines the final product's transparency. To guarantee optimal color quality, we utilize advanced instruments to evaluate surface smoothness, transparency, and color accuracy across various sample types. These state-of-the-art machines facilitate precise analysis and control of colors, allowing us to refine and standardize hues effectively.
Color consistency in silicone rubber keypads is managed through meticulous pigment control during molding. While we primarily use the Pantone system for color matching, we can also align colors with plastic samples or color chips. Due to silicone’s unique properties, color variations can occur under different lighting conditions—a phenomenon known as metamerism. In such instances, we make precise adjustments to the pigment formula to ensure the desired color is achieved. Once finalized and approved, the pigment formula is fixed to maintain uniform color throughout production and the product's lifespan.
We excel in accurately matching pigments for our molded parts and silicone-based inks. Our silicone-based inks form a permanent bond with silicone products, and we ensure exacting standards by mixing and measuring inks within precise tolerances. Our high-quality pigments, sophisticated equipment, advanced software, and skilled laboratory technicians collectively enhance color consistency, repeatability, and expedite delivery times for color matching.
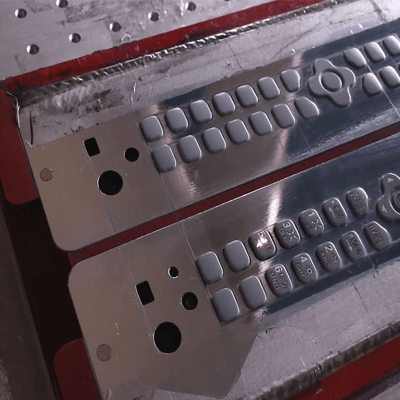
Embossed/Engraved Key-Tops
Embossing or engraving silicone key tops directly is the most cost-effective and durable method for creating legends. This approach not only offers economic advantages but also ensures that the markings resist wear over time and supports features such as backlighting with clear silicone. For added versatility, insert molding or flow molding techniques can be used to incorporate various colors into the key tops.
However, there are some considerations to keep in mind. Embossed or engraved legends can trap dirt in their recesses, which may impact the long-term cleanliness of the key tops. Additionally, since the legend is integral to the mold design, any changes or updates to the markings require significant modifications to the tooling, which can be costly. The tooling process imposes constraints on the design, affecting the size, depth, and line thickness of the legends. Embossed legends generally offer more flexibility in tooling compared to engraved ones, though both methods have specific limitations as outlined by the design parameters.