LSR overmolding is an advanced two-shot plastic injection molding technique that integrates two distinct yet complementary thermoplastic materials into a single, cohesive part. The initial injection, known as the substrate, usually consists of a rigid plastic that forms the structural foundation. This substrate is designed to accept the second material, which is typically a softer, more flexible material such as rubber or thermoplastic elastomer (TPE).
The second injection, known as the overmold, is selected for its flexibility and ergonomic properties. This material is applied over the substrate through a process of mechanical or chemical bonding, resulting in a seamless final product. The combination of the rigid substrate and the flexible overmold yields a product that offers both structural strength and enhanced comfort.
This technique is particularly effective for producing silicone keypads, as it enhances their functionality, aesthetics, and usability. By leveraging the durability of the substrate and the comfort of the overmold, overmolding creates superior silicone keypads that meet high standards of performance and user experience.
Advantages of LSR Overmolding for Silicone Keypads
1. Reduced Assembly Costs: Overmolding streamlines production by combining components in a single molding process, minimizing the need for manual assembly. This integration reduces the risk of errors and lowers overall unit costs, ensuring precision and efficiency through repetitive manufacturing.
2. Enhanced Ergonomics and User Experience: By incorporating soft, rubbery layers into products like handles and electronic devices, overmolding significantly improves comfort and usability. This technique is particularly effective for creating multi-colored designs and adding soft grip layers, which enhance both functionality and visual appeal.
3. Design Flexibility: Unlike traditional methods that rely on CNC milling or assembly with fasteners and adhesives, overmolding enables the creation of complex, integrated shapes in a single part. This flexibility allows for more innovative and intricate designs without the constraints of manual assembly.
4. Improved Quality and Performance: Overmolding enhances the durability and performance of products, such as silicone keypads, by offering features like waterproofing and isolation of metal contact pins. This process ensures reliable performance in demanding conditions and improves overall product quality.
Utilizing LSR overmolding for silicone keypads delivers exceptional durability, functionality, and design versatility, resulting in high-quality products tailored to meet diverse application requirements.
Why Choose Rockeypad for Your Custom LSR Over-Molding Service?
Extensive Production Capacity: Our state-of-the-art facility houses over 10 LSR injection machines ranging from 60 to 160 tons, ensuring robust production capacity and flexibility. Utilizing advanced control technology, we deliver high-quality LSR products swiftly, tailored to meet specific customer requirements, including those for silicone keypads.
Biocompatibility and Performance Properties: We rigorously select and test our LSR materials to meet stringent medical and healthcare biocompatibility standards for components intended for human contact. Our manufacturing process occurs in an advanced Class 8 cleanroom, ensuring a sterile environment for producing medical-grade LSR components. Adhering to international standards like ISO 9001, our LSR components, including silicone keypads, are safe and reliable for medical applications.
Multi-Material Molding Expertise: We excel in multi-material molding, incorporating two-shot, insert, and over-molding techniques. This capability allows us to combine different LSR materials with other materials in a single mold, enabling intricate and diverse product designs. This flexibility ensures we can meet various performance requirements, customize colors, streamline manufacturing processes, and enhance product quality, making us a leader in the LSR injection molding industry, particularly for silicone keypads.
Precise Control: Our high-precision injection molding machines and advanced control systems monitor and adjust key parameters like temperature, pressure, and speed in real-time. This ensures stable and consistent LSR injection, guaranteeing uniform product dimensions and quality. Whether for small-batch or large-scale production, we maintain a high level of accuracy throughout the manufacturing process, meeting the exacting demands for high-quality LSR products, including silicone keypads.
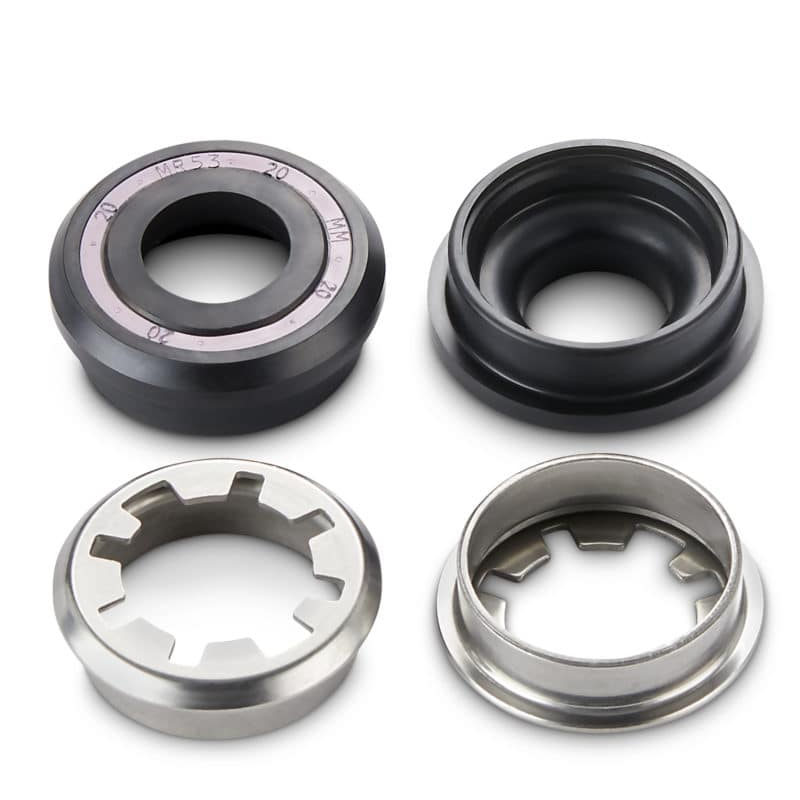
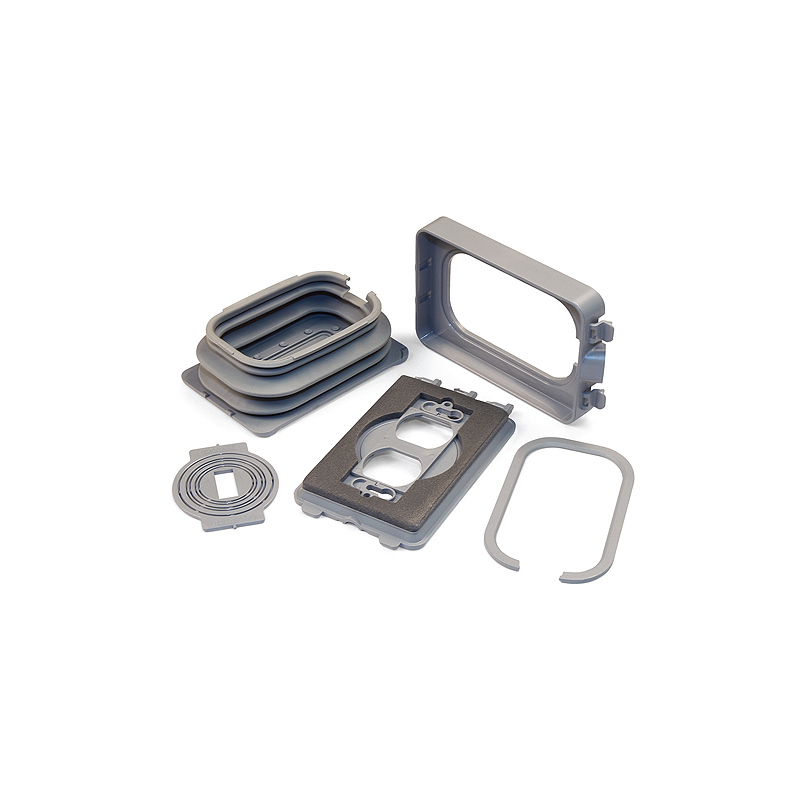
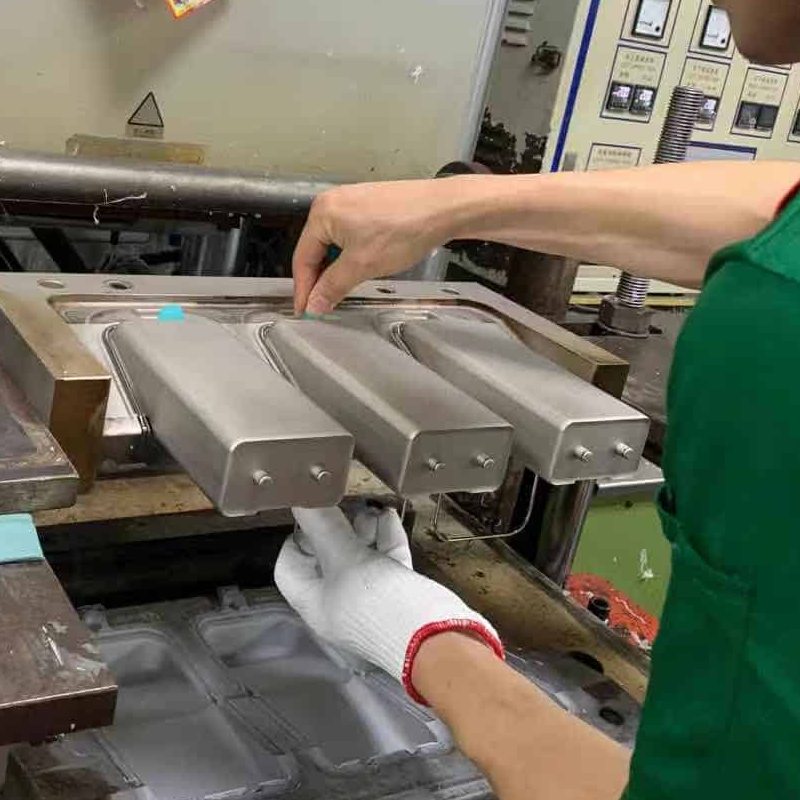
Materials Utilized for LSR Overmolding
At Rockeypad, we offer a comprehensive selection of materials for LSR overmolding projects, tailored to accommodate various geometries, complexities, and specific project requirements. Our materials are categorized into four key groups:
1. Rigid Plastics: Designed for durability and strength, these materials are ideal for structural components. Our offerings include ABS, Polypropylene, Polycarbonate, Acrylic, Nylon, POM, PTFE, PBT/PBT-PC, PEEK, HDPE, PVC, PPS, PI, PAI, UPE/UHMW, PVDF, and ULTEM (PEI).
2. Flexible Plastics: Suitable for applications requiring flexibility and cushioning, our flexible plastic options include PS, PET, EVA Foam, EPS Foam, and PU Foam.
3. Rubber Plastics: Providing excellent elasticity and resilience, these materials are ideal for components needing a soft touch and enhanced durability. We offer TPU and Silicone Rubber.
4. Specialty Materials: For projects with unique demands, we supply specialty materials such as biocompatible plastics for medical applications and high-temperature resistant materials for industrial uses. These specialized options ensure we meet the most stringent and specific project criteria.
Our diverse material selection allows us to deliver customized solutions that meet the precise needs of your LSR overmolding projects.
Tolerances
Mold Type | Dimensional Tolerance |
Substrate Molds | ± 0.02 mm, with an included resin tolerance that can be greater but no less than 0.02 mm |
Thermoplastic Overmolds | Tolerances consistent with substrate molds |
LSR Overmolds | ± 0.02 mm |
Finishing Options
Painting: We offer surface painting in standard colors or Pantone matches, including primer and topcoat. Masking services are available, as well as EMI (copper) paint applications.
Mold Texturing: Our texturing services create various finishes on molds, including matte, swirls, patterns, and lines, which are reflected on the final product.
Threaded Inserts: We install standard threaded inserts in both UNF and metric sizes, ensuring durability and reliability in your components.
Laser Engraving: This service allows for precise engraving of part numbers, designs, logos, or other specified details directly onto your parts.
SPI Finishes: We offer a range of SPI finishes, from Grade 3 diamond/high polish to 320 stone low polish, to achieve the desired surface quality.
Pad Printing: An ink-based design can be applied to the surface of your parts, providing clear and durable markings.
Standard Finish: For non-cosmetic interior surfaces, we provide a finish based on the mold's geometry, ensuring functionality without additional cosmetic enhancements.
As Molded: This option leaves the mold 'as is' without secondary texturing or polishing, maintaining the original molded surface.
Applications of LSR Overmolding
Medical Devices: LSR overmolding is utilized to enhance medical devices by integrating soft-touch grips and ergonomic handles onto rigid components, significantly improving patient comfort and usability. This technology ensures the production of high-quality, user-friendly medical tools.
Automotive Industry: In automotive applications, LSR overmolding is applied to plastic or metal parts to create weather-resistant seals, vibration-dampening components, and advanced gaskets. This process enhances the durability and performance of automotive components, ensuring they meet rigorous industry standards.
Electronics and Electrical: LSR overmolding is essential for encapsulating and protecting sensitive electronic components, resulting in durable connectors and improved product aesthetics. This technique is particularly effective in creating reliable and visually appealing electronic devices, including silicone keypads used across various applications.
Kitchen & Bath: LSR overmolding technology is employed for kitchen utensils, bathroom accessories, faucets, showerheads, washing tools, and cabinet hardware. This process provides added comfort, anti-slip properties, and enhanced durability, greatly improving the user experience.
LSR overmolding effectively combines the benefits of liquid silicone rubber with other materials, resulting in products with superior performance, aesthetics, and functionality. By leveraging LSR overmolding, we enhance the quality and versatility of products like silicone keypads, ensuring they meet the highest standards for durability and usability across diverse applications.