What Is LSR Injection Molding
LSR, or Liquid Silicone Rubber injection molding, is a highly efficient process for producing high-quality silicone components in medium to high volumes. This process utilizes low-viscosity silicone elastomer provided in two-part kits, which are injected into the molding machine's injection unit using high-precision pumps. Silicone’s bio-inert and biocompatible nature makes it a preferred material in the medical device industry, and its high-temperature resistance and superior physical properties make it ideal for automotive and industrial applications.
LSR silicone keypads, also known as Liquid Silicone Rubber keypads, keyboards, or buttons, are manufactured using high-precision Liquid Silicone Rubber injection molding. These keypads, made from high-transparency, high-tear strength silicone with excellent resilience and resistance to water, heat, and cold, are widely utilized in medical, industrial, instrumentation, and communications equipment. While many silicone keypads are produced through compression molding due to its cost-effectiveness and ability to produce quality keypads using good metal steel, the superior properties of liquid silicone rubber have led to its increasing popularity among customers.
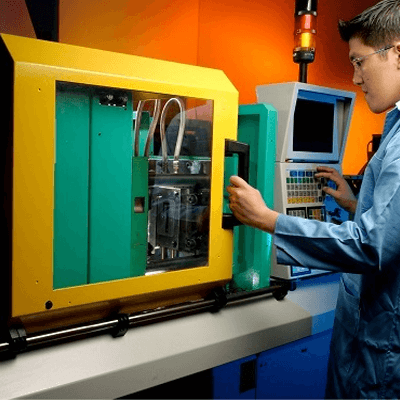
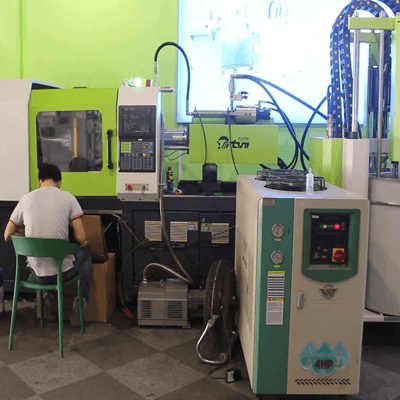
Features of LSR
At Rockeypad, we specialize in liquid silicone rubber (LSR) injection molding, leveraging advanced manufacturing processes to produce high-quality parts and sheets. Our platinum cure silicone compounds are ideal for various applications due to the following key features:
- Wide Hardness Range: LSR offers a durometer Shore A range from 10 to 80, accommodating diverse application needs.
- Broad Operating Temperature: Capable of functioning effectively from -58°F to 392°F (-50°C to 200°C), LSR is suitable for extreme conditions.
- Excellent Elongation Properties: LSR demonstrates superior flexibility and stretchability.
- Outstanding Electrical Insulation: Ideal for applications requiring high electrical insulating properties.
- Superior UV and Ozone Resistance: Perfect for outdoor use due to its resistance to ultraviolet rays and ozone.
- Effective Environmental Sealing: Provides exceptional sealing capabilities for outdoor environments.
- Reliable Submerged Sealing: Meets IP67 and NEMA 6 standards for underwater sealing applications.
- Flame Retardant Options: Available in formulations with UL 94HB and UL 94V-0 flame ratings for enhanced safety.
- Medical Grade Compliance: Certain LSR products meet stringent FDA and USP Class VI requirements, making them suitable for medical devices.
- Low-Temperature Cushioning: Performs well in cold environments, as evidenced by cold drop tests.
- Color Versatility: Available in various standard and custom colors for molded parts and sheets.
Electrical Properties of Liquid Silicone Rubber:(values shown are approximations) | ||
Content Resistance | 20 - 200 ohms | |
Contact Rating: | 30 mA at 12 VDC | |
Contact Bounce: | <20 mS, typical | |
Insulation Resistance: | >100 M ohms at 500 |
Our state-of-the-art facilities support a full range of services, from rapid prototyping to large-scale production of precision components. Whether you need intricate prototypes or mass-produced parts, our expertise in LSR injection molding ensures superior quality and performance.
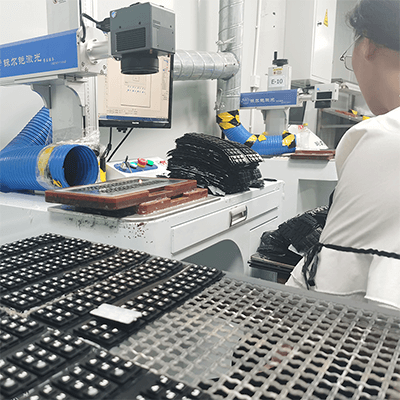
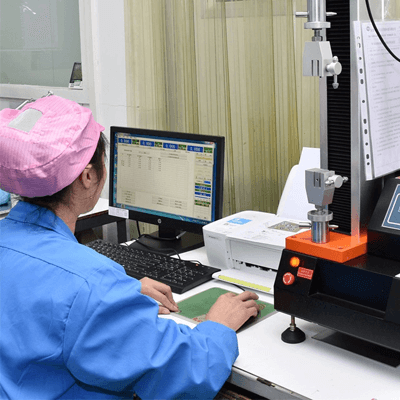
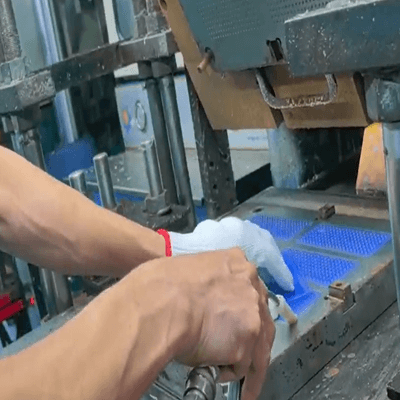
Silicone Rubber Injection Molding Process
- Material Preparation: The process starts with the preparation of two separate components, Part A (base material) and Part B (catalyst), which are pumped through hoses to a static mixer. An additional hose introduces color. The mixed components are fed into the injection molding barrel through a shut-off valve, ready for molding.
- Sealing Against Molded Parts: Once the silicone material is inside the barrel, a shot of the cooled mixture is injected into the mold. The nozzle seals firmly against the liquid silicone rubber to ensure proper injection.
- Injection: The nozzle shut-off valve opens, and a precise shot of cooled liquid silicone is injected into the hot mold, which is maintained at temperatures between 275°F to 390°F.
- Barrel Retraction: The nozzle shut-off valve closes, and the barrel retracts from the mold. The screw mechanism prepares the next measured shot of cooled liquid silicone for the following injection cycle.
- Cycle Repetition: Upon completing the injection cycle, the mold opens, allowing the removal of the molded part and any flashing, either automatically or manually. The mold then closes to repeat the procedure.
- Post-Molding Process: After the molded article is removed, post-molding processes such as demisting, post-curing, inspection, and packing are performed to ensure the final product meets quality standards.
Advantages of Silicone Injection Molding
- High-Volume Production: Leveraging advanced LSR materials, silicone injection molding facilitates the cost-effective production of intricate parts in large volumes.
- Minimal Contamination Risk: Liquid injection molding (LIM) utilizes automated machinery, significantly reducing human interaction with materials. Unlike the labor-intensive process of compression molding, LIM offers a lower risk of contamination. Fully automated injection molders and ISO-certified clean rooms further ensure a hygienic production environment.
- Swift Cycle Time: The cycle time for LSR components is influenced by mold temperature, material delivery, component geometry, vulcanization properties, and curing material chemistry. Preheating the injection barrel and cold runner to 40-80°C accelerates the curing process for two-part, platinum-cured LSRs.
- Flash and Waste Elimination: Utilizing molds with minimal runners and flash-free operation virtually eliminates material waste, ensuring efficient and sustainable production.
Why Choose Rockeypad for LSR Injection Molding Services?
- Material Versatility: Selecting the right material is crucial for flexibility and customization in product development. LSR provides customers with the ability to tailor their products to specific needs.
- Extreme Temperature Resilience: LSR maintains its properties across a broad temperature range, from –76°F to +365°F, making it ideal for parts that endure diverse temperature conditions.
- Wide Range of Applications: With its extensive durometer spectrum and compatibility with various additives, LSR can be adapted for numerous applications, enhancing its properties as needed.
- Resilience to Environmental Factors: LSR is highly resistant to chemicals, water, oxidation, and compression set, ensuring a long service life and reduced maintenance requirements.
- Medical Suitability: LSR’s biocompatibility, non-toxicity, and resistance to bacterial growth make it particularly suitable for medical equipment.
- Electrical and Chemical Resistance: LSR’s robust resistance to high electrical current and harsh chemicals makes it an excellent choice for high-voltage environments.
- Industry-Specific Applications: Beyond medical equipment, LSR is beneficial for a wide range of industry-specific parts, demonstrating its versatility and broad applicability.
- Expert Design Support: Rockeypad's team excels in the innovative and precise design of LSR molded parts, providing comprehensive customer support throughout the entire process.
Applications of LSR Injection Molding
Liquid silicone rubber (LSR) injection molding is extensively utilized across various industries, including medical devices, healthcare, automotive, infant care, consumer food and beverage, appliances, electronics, and industrial sectors.
Medical Devices
LSR's inert properties, biocompatibility, and stability under rigorous conditions make it highly suitable for medical applications. Many life sciences products incorporate components that require intricate details, tight tolerances, and small part geometries, all while ensuring high cleanliness standards. Common applications in the medical field include respirator masks, valves, diaphragms, surgical instruments, and drug delivery devices.
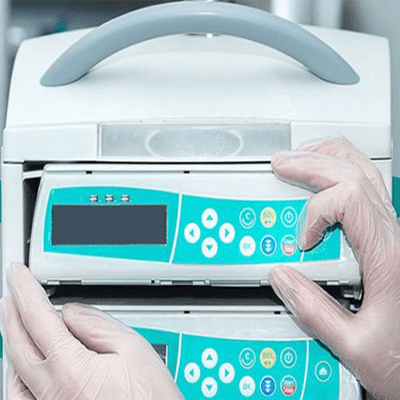
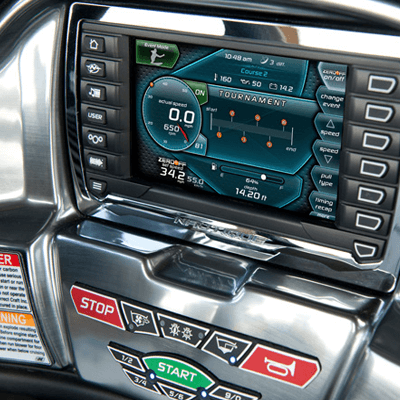
Automotive
In the automotive sector, LSR is valued for its outstanding performance under extreme temperatures and UV light exposure. It is used in a variety of components such as wire harness seals, connectors, bellows, gaskets, vibration dampeners, housings, and sensors.
Industrial Applications
For industrial products that must endure challenging environments, LSR is ideal. It is used in valves, gaskets, and sealed housings for safety devices such as smoke detectors. In sensitive applications like furnaces and gas water heaters, LSR’s stability is crucial. It withstands chemicals and high heat while maintaining its form, ensuring reliable performance in manufacturing equipment, safety devices, and other projects where durability and reliability are paramount.
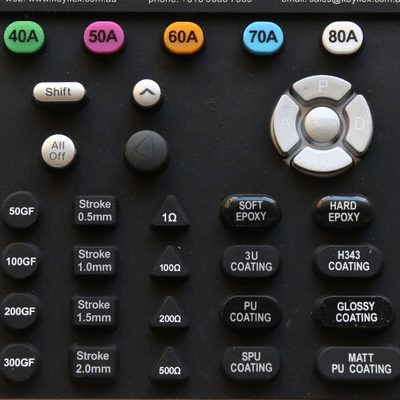
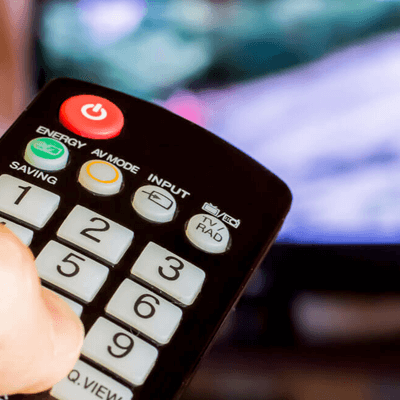
Consumer Products
LSR is a preferred material for consumer products due to its versatile properties. It is used to create watertight barriers, bacteria-resistant showerheads and faucets, vibration-resistant sealed housings for hygiene products, soft surfaces for headphone and hearing aid tips, and safe baby bottle tips. Additionally, LSR's performance in varying environments and temperature ranges makes it suitable for appliance components like valves, gaskets, and diaphragms.